Danner
process equipment for glass tubing drawing |
¡¡
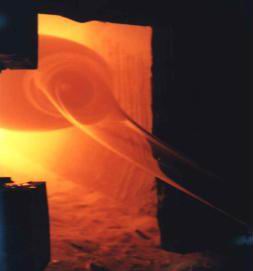
Glass
tubing is drawn out from the tip of the sleeve
|
1. |
Preface |
|
Danner
process, which is a horizontal glass tubing technology, is the
most usual choice for soda-lime, lead and borosilicate glass
tubing drawing. This process provides good accuracy in diameter,
thickness; bow and ovality as well as lopside, thus the most glass
tubing production lines in the world were and are equipped with
Danner process and its machines.
Beijing
Quarts V. Glass Co., Ltd. supply either single machine or complete
tubing drawing line, meanwhile Vello process equipment and whole
line are also available to be provided. |
¡¡
2. |
¡¡
Components
of Danner Process Equipment |
|
The
Danner process consists of a trough at the end of forehearth, a
Muffle in which a hollow refractory mandrel aslant installed and
called as Sleeve, a Sleeve driver, tubing running alley and a
Danner drawing machine together with cutter(s) as well as a
precise cutting & glazing machine. The accessories of Danner
tubing line are combustion system for Muffle, temperature control
system of trough and Muffle as well as dimensions detectors for
outside diameter and wall thickness, glass defects some cases. |
¡¡
3. |
¡¡
Muffle |
|
|
The
Muffle is a kind of oven with two layers, the first layer is made
of Silicon Carbon (SiC) plates that form an oval shape chamber, in
center of which the sleeve locates. The molten glass from
forehearth through a refractory gate flows out of the trough and
falls down as glass ribbon to the sleeve. |
¡¡
4. |
¡¡
Sleeve
part |
|
A
refractory mandrel plays a role of the sleeve that fixes on the
sleeve shaft. The size of sleeve depends on the size of the tubing
to be drawn. The sleeve shaft is a bigger and longer enough
heat-resistant steel axle with a straight hole in the center for
inflating air.
Material: Sillimanite
Dimension: Length
1500mm
Diameter:270, 300, 330mm |
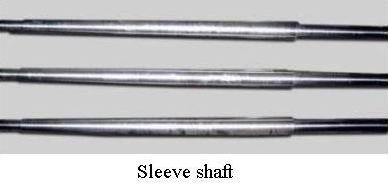 |
¡¡
5. |
¡¡
Sleeve
driver |
|
The
sleeve driver is used to drive the sleeve shaft with sleeve
rotating.
Its main body is water cooled, the sleeve shaft in it is driven
by a motor and the worm-gear box. There are several adjusting
parts on the sleeve driver respectively, at the base of the
support frame of the driver there are hydraulic cylinders to move
the sleeve driver up/down and left/right at the initial stage of
installation.
Main drive: 3.0Kw, 380V, 50Hz
Speed: 4 rpm (min.)¨C15 rpm (max.)
Diameter of chuck: 100 mm
(75mm also available)
Number of rotation: 4¨C15 rpm, adjustable
Adjusting angle: 0¡ã¨C15¡ã, adjustable
Vertical stroke: 510 mm, adjustable
Back and forth stroke: 260 mm, adjustable
Lateral stroke: ¡À70 mm, adjustable
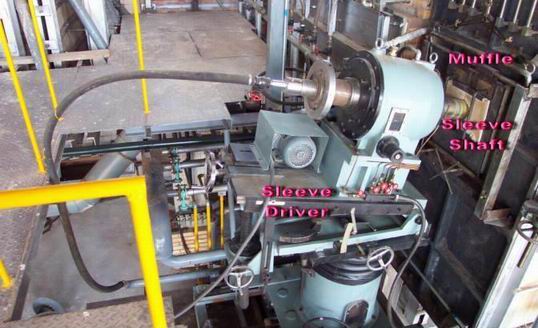
|
¡¡
6. |
¡¡
Tubing
Running Alley |
|
The
tubing running alley comprises two parts. The
insulation cover made of steel plates eliminates the influence of
environment temperature. The cover and pit make a closed
tunnel to be the first part. The other part is running alley that
holds the glass tubing for a relative long distance mostly in the
closed cases. Many rollers inside of the alley are free rotating
by means of air bearings and playing the role of the tubing
brackets.. |
|
¡¡ 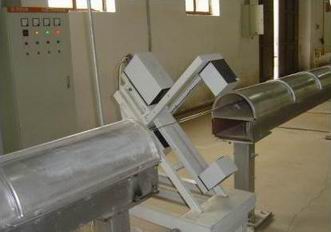
Tubing Running Alley and X-Y laser OD
detector
Rollers inside of the alley |
¡¡
7. |
¡¡
Drawing
Machine (Danner Machine) |
|
The
Drawing machine usually includes cutting machine, which can be
driven by the same motor used for the drawing machine or an
independent motor. The drawing motor drives several rollers that
are located at two layers shown as the photo below. The both upper and lower
belts ring are hooped on the rollers. The tubing is running
forward in the gap between both rotating belts. The rotating of
the belts always enables tubing moving to the cuter.
At the entrance of the drawing machine there are three guide
rollers, two vertical rollers and one horizontal
roller guides the tubing to the gap of belts.
The
cutter can be single or double according to tube size and the line
speed of tubing drawing.
After
cutting it is a sorting machine to reject NG tubes based on laser
OD detector signals in the case of over tolerance of outside
diameter.
Main drive unit: 3.0Kw, 380V, 50Hz
Glass tubing diameter:4.0¨C40mm
Drawing speed:25-200mm/min.
Cutting length:1000¨C1800mm |
|
¡¡
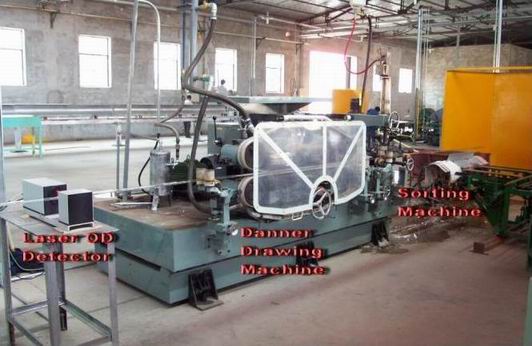
The
Drawing machine following with cutter and sorting machine |
¡¡
8. |
¡¡
Precise
cutting and Glazing |
|
The
tubes after sorting are qualified tubes in diameter, which are
moving to re-cutting and glazing machine through the front
conveyer (three segments) with line up machine.
The re-cutting is done by several pairs of burners at the both
ends of the machine, i.e. both tube ends together are precisely
cut with a pair of sharp and thin discs made of special steel. The
cut tubes then move to be glazed by 6 pairs of glazing burner.
After glazing the hot tubes should be cooling down on a cooling
conveyer, then the tubes can be packed.
Main drive unit: 1.5Kw ´2, 0.4 KW 380V,
50Hz
Length:1200mm¨C1800mm
Precise cut and glazed glass tubing diameter:10¨C40mm
Cutting length:1200¨C1700mm
Full length of the machine:11m
We
also supply the front conveyers installed before precise cutting
machine and
cooling conveyer after glazing machine. |
¡¡
9. |
¡¡
Electric
part |
|
(1)
Automatic control system
¢Ù Muffle roof temperature control system
¢Ú Muffle chamber temperature control system
¢Û Inflating air pressure control system
(2)
Automatic sorting system
Laser O.D. measuring system and sorting system
General type (single direction) and X-Y type are available
(3)
Automatic synchronizing system for any tubing specification
All motors of conveyers and re-cutting &
glazing machine after cutting should be synchronized to ensure no
touch between tubes on the conveyers to avoid scratches.
(4)
Monitoring system
Tubing catenary monitoring system by ITV.
(5)
Measuring system
¢Ù Measuring speed of sleeve driver
¢Ú Measuring speed of drawing machine
¢Û Measuring cut numbers, NG counter, OK counter
after the first cutting
¢Ü Measuring Muffle temperature at 5 points
¢Ý Measuring
inflating air pressure |
|
|